CMP Slurry Blending & Delivery
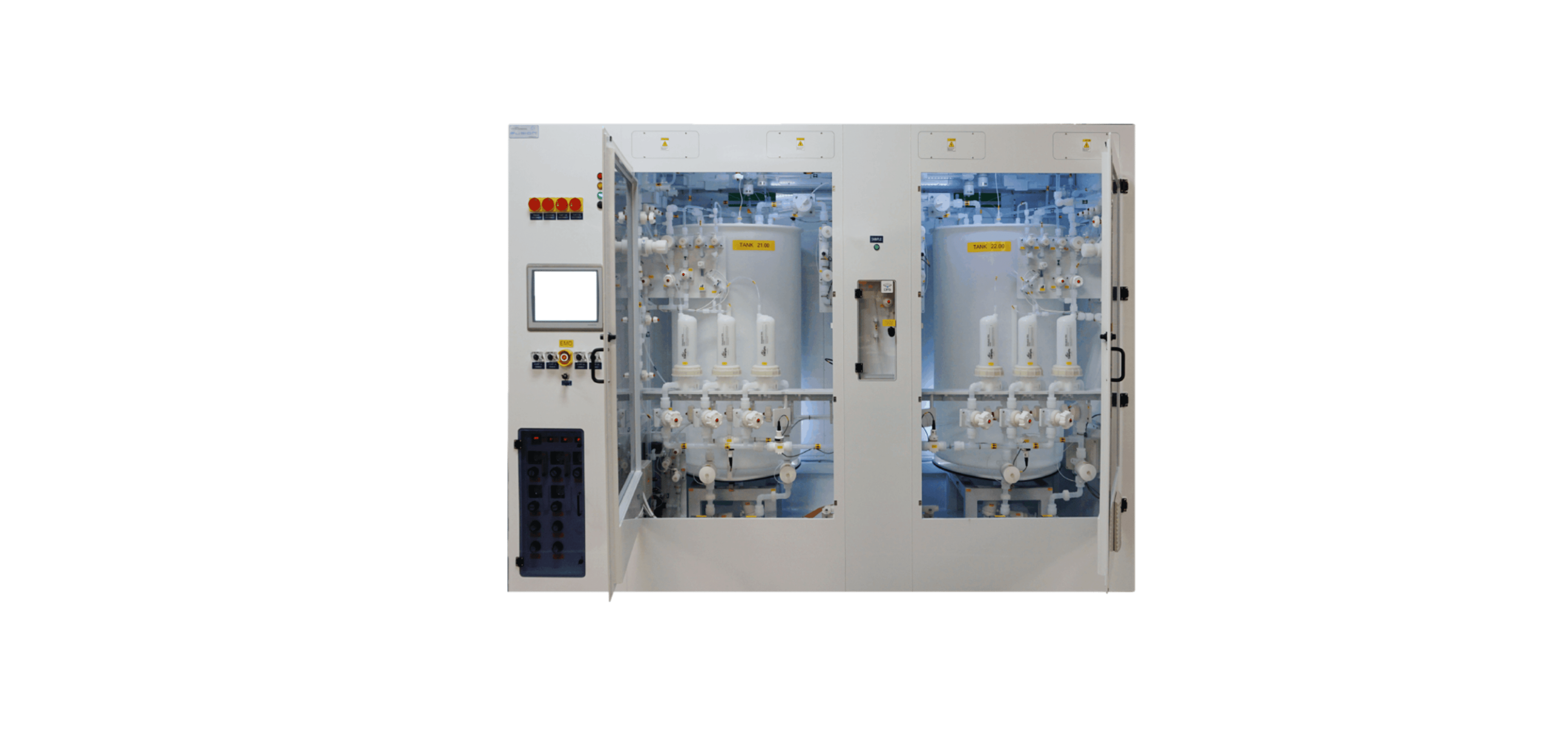
CMP Slurry Blending & Delivery
Remove expensive labor-intensive offline metrologies and manual process adjustments
Semiconductor fabs have increasingly tight upper and lower control limits (UCL / LCL) for a number of critical process parameters. These parameters include concentration specific related functions, and many others as associated with CMP slurry blending and distribution operations of a given critical chemical action.
To achieve this there have been major advances in metrology, varying in areas and principles; but many today are only offline measures or verifications, which are used to meet the required precision and accuracy for these control limits.
To eliminate the need for offline instruments, Exentec has a proven practice of chemical mechanical polishing characterization, where it is possible to use various metrology devices, or combinations of these devices, to achieve the best-in-class in-line metrology driven control with the highest level of precision.
Exentec can use this concert of instruments to achieve real-time online results that have been proven to meet or exceed the levels seen by many offline methods.
Advantages
- Higher blend accuracy and real-time control
- Maximim uptime
- Fully automated system
- Low cost of ownership
- Flexible and user-friendly HMI
- System and/or component redundancy to maximize production uptime
- Automated system flushing
- Space efficient designs
- Full blend configuration and manipulation
High Purity Chemical Systems
We offer equipment, field support service and technical expertise to meet various application needs of high purity fluid delivery, chemical blending and state-of-the-art CMP slurry systems for semiconductor manufacturing and other high-tech industries.
Chemical Offload
The Exentec Titan™ Transfer and Offload System automatically transfers an aqueous chemical from the tanker offload cabinet to the main distribution tanks.
Chemical Distribution
Exentec offers equipment, support service and technical expertise to meet application needs in the design and manufacturing of high and low purity chemical distribution systems.
In-Line Blending
Exentec's patented on-demand in-line chemical blending and supply of chemical solutions technology can accommodate on-demand dynamic change in flow rates by the end users or points of use while maintaining precise blend accuracy.
Chemical Generation
Exentec's NH4OH on-site chemical generation technology helps semiconductor fabs to significantly reduce their overall chemical supply costs, improve resiliency and increase ecological sustainability.